Aridom82
Learning addict
So this just happened: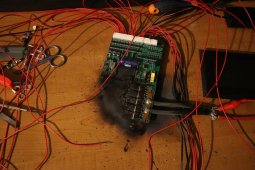
This is the connection diagram i had:
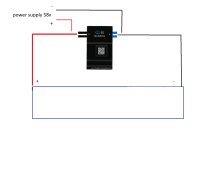
The red wires were connected properly, the bms was up and running, i had connected the power supply to start charging the batteries and after i enabled charge via the app the bms exploded like fireworks. I hope my cells are still ok. I dont know what happened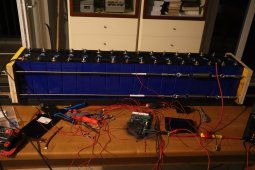
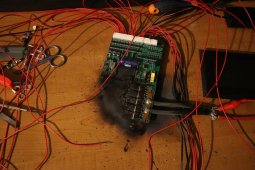
This is the connection diagram i had:
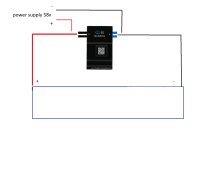
The red wires were connected properly, the bms was up and running, i had connected the power supply to start charging the batteries and after i enabled charge via the app the bms exploded like fireworks. I hope my cells are still ok. I dont know what happened
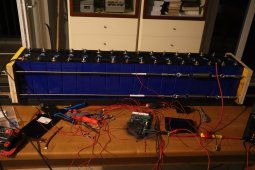