Here are some better closeups of each enclosure going left to right.
GND wires are all 1/0 Al. Everything else is 300 MCM Cu or 500 MCM Al, with the exception of the wires going through the wall in the junction box to the 200A shop sub-panels. Those are 3/0 Cu for L1, L2 and N. Oh, and the N for the solar sub-panel is 3/0 Cu as well. Those SBs don't really use N, so I figured that would be plenty.
Meter base with the new feed. Got 500 MCM L1 and L2 along with a 350 MCM Neutral coming up on the left. You can also see the #4 bare copper wire going to the ground rods. Then on the right side, is my 300 MCM L1, L2 and N leaving:
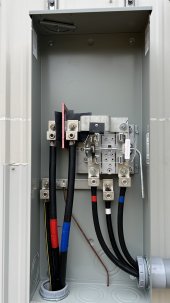
Next is the disconnect switch. This is where N and GND are bonded, both to each other as well as to the enclosure. You see the 3 cables coming from the meter base entering on the left, and you see wires existing to the right. The 2nd set of Red/Blue cables you see at the bottom is from the Solar sub-panel, the other set goes to the grid side of the transfer switch.
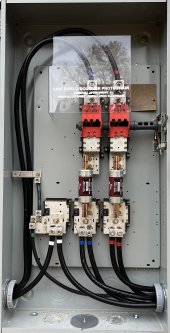
Next stop is the transfer switch. The pic below is from before I landed L1 and L2 from the solar sub-panel in the disconnect enclosure. Here you can see that GND is bonded to the enclosure as well:
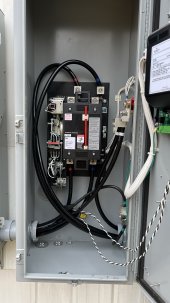
And finally, we have the "junction box":
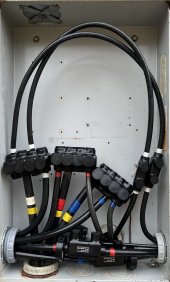
The 4 GND wires are hiding behind the Polaris splice connector at the front bottom center. You can also see a #6 GND wire going up to ground the enclosure.
So all 4 enclosures hanging on the shop wall have their enclosures grounded. What you don't see, is that the GND wire coming from the 200A sub-panel inside the shop, is tied to the sub-panel enclose and also has a #6 bare copper going to the dual 8' ground rods.
Here's an old drawing I did before installing these cabinets on my house back in 2016:
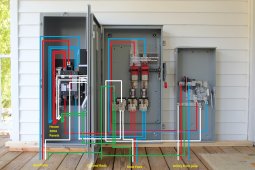
If you still see something I need to correct, I'm all ears. Now is the time to do it before it gets energized next week.
GND wires are all 1/0 Al. Everything else is 300 MCM Cu or 500 MCM Al, with the exception of the wires going through the wall in the junction box to the 200A shop sub-panels. Those are 3/0 Cu for L1, L2 and N. Oh, and the N for the solar sub-panel is 3/0 Cu as well. Those SBs don't really use N, so I figured that would be plenty.
Meter base with the new feed. Got 500 MCM L1 and L2 along with a 350 MCM Neutral coming up on the left. You can also see the #4 bare copper wire going to the ground rods. Then on the right side, is my 300 MCM L1, L2 and N leaving:
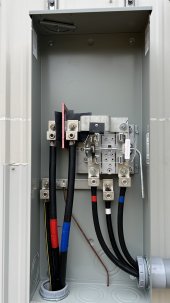
Next is the disconnect switch. This is where N and GND are bonded, both to each other as well as to the enclosure. You see the 3 cables coming from the meter base entering on the left, and you see wires existing to the right. The 2nd set of Red/Blue cables you see at the bottom is from the Solar sub-panel, the other set goes to the grid side of the transfer switch.
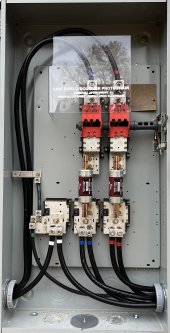
Next stop is the transfer switch. The pic below is from before I landed L1 and L2 from the solar sub-panel in the disconnect enclosure. Here you can see that GND is bonded to the enclosure as well:
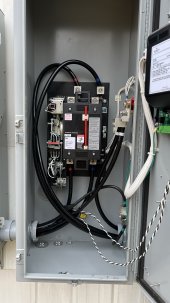
And finally, we have the "junction box":
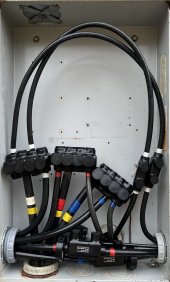
The 4 GND wires are hiding behind the Polaris splice connector at the front bottom center. You can also see a #6 GND wire going up to ground the enclosure.
So all 4 enclosures hanging on the shop wall have their enclosures grounded. What you don't see, is that the GND wire coming from the 200A sub-panel inside the shop, is tied to the sub-panel enclose and also has a #6 bare copper going to the dual 8' ground rods.
Here's an old drawing I did before installing these cabinets on my house back in 2016:
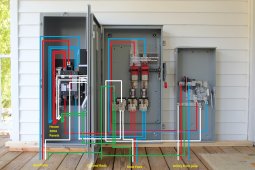
If you still see something I need to correct, I'm all ears. Now is the time to do it before it gets energized next week.
Last edited: