fmeili1
Solar Enthusiast
Finally after 18 month I've completed the installation of my DIY off-grid system. It was an incredible amount of work, much much more than previously expected.
Tomorrow will be the final inspection of the cities building division and on Friday the inspection of the power company - I'm very nervous...
Here are the key points:
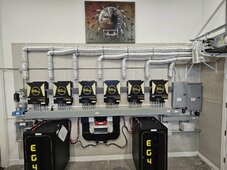
For final testing, I've used the system for the last 5 days and everything is working so far as hoped. The batteries have about 63% SOC remaining in the morning before new solar production begins (this will change in summer for sure). Between 11am and 12pm the batteries are fully re-charged.
Because of the implemented ducted mini spit the AIO's running very nice cool and because of the modded fans, they are really quiet now.
The next charts showing an example of a 24h cycle while testing (full PV production between 6:30am and about 12pm until the batteries are fully re-charged):
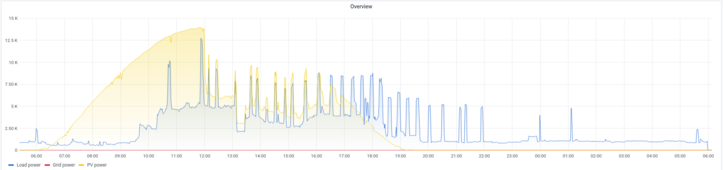


Load and consumption situation of the house:
Unexpected challenges / missed considerations while building:
I am totally amazed and very pleased that my LED pulsing/flickering problems are completely gone - without doing anything! While in building phase, I've noticed the LED pulsing problem a couple of times and I thought many hours about how to solve it. I have no idea why this problem completely disappeared, independent if solar production or not, clouds or not, battery charging or discharging, high or low load,...
I'll update this thread from time to time with new pictures, findings, data, issues, etc.
Tomorrow will be the final inspection of the cities building division and on Friday the inspection of the power company - I'm very nervous...
Here are the key points:
- Single family home with 200A service and about 2100sqft living space, attached 2 car garage and RV garage
- Central heat pump for cooling and heating, everything electrical, no natural/propane gas, no wood fireplace
- Off-grid system with 39kW inverter power, grid only as backup if really required (disconnected most of time via remote controlled contactors).
- Permission to treat it as a "generator solution" with a manual transfer switch and I have the permit to have a permanent AC-in connection to the grid, independent of the transfer switch position!
- 18.5kWp solar bifacial modules 460Wp, 40 PV modules organized in 8 strings, strings with 4, 5 and 6 modules in series (no parallel modules), most modules on concrete tiled sloped roof (8 on RV garage flat roof), PV module orientation is 17x south, 11x north, 6x east, 6x west (not ideal roof for solar).
- LFP batteries (40kWh are allowed, organized in two separate racks)
- Emergency shutdown features for many possible failure scenarios
- Fully integrated in existing smart home to implement "smart" energy management and remote monitoring/controlling
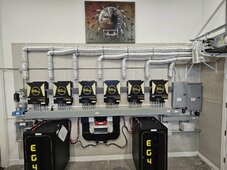
For final testing, I've used the system for the last 5 days and everything is working so far as hoped. The batteries have about 63% SOC remaining in the morning before new solar production begins (this will change in summer for sure). Between 11am and 12pm the batteries are fully re-charged.
Because of the implemented ducted mini spit the AIO's running very nice cool and because of the modded fans, they are really quiet now.
The next charts showing an example of a 24h cycle while testing (full PV production between 6:30am and about 12pm until the batteries are fully re-charged):
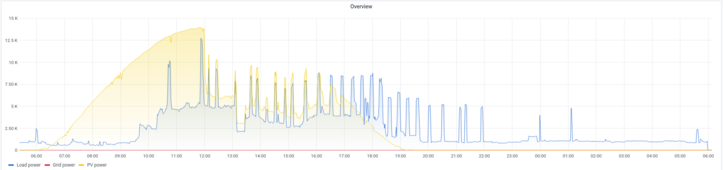


Load and consumption situation of the house:
- 21,000kWh per year consumption
- 114kWh highest peak consumption per day (usually end of July or beginning of August)
- Highest consumption between May and August (2,000kWh to 3,000kWh per month)
- High power consumption devices sorted by power
- Central heatpump: 5,800W (max. 7kW, <=15kW inrush)
▪ Dryer: 5,200W
▪ Water heater: 4,470W
▪ Wall oven: 3,500W
▪ Coocktop large field: 3,300W
▪ RV garage mini split: 2,500W
▪ RV parked in the driveway: 2,000W
▪ Microwave: 1,700W
▪ Coocktop 3 small fields: 3x1,400W
▪ Washer (front loader with heating element): 1,200W
▪ Pool pump: 1,200W - High energy consumption devices sorted by runtime:
▪ Pool pump: 8 hours only on daytime
▪ Central heatpump: in high summer days it runs about 60%-90% of the time constantly (60% at night), in winter time it runs about 20%-30% of the time - Power requirements so far:
▪ house idle consumption is about 500W
▪ AIO idle/self consumption is about 550W for all six units
▪ while pool pump is running 8-9h over the whole day the base house load is about 2000W total
▪ never seen more than 24kW power consumption at a time – but it may happen
▪ possible worst case could be: 2000W idle with pool pump + 5000W heatpump + 4500W water heater + 3500W oven + 6500W for 3 coocktop fields + 200W dryer + 2500W RV garage mini split + 2000W RV in driveway connected to the house + 1200W washer = 32.5kW is still below rating of 39kW with reserve for e.g. toaster, water cattele, microwave, tools, etc.
Unexpected challenges / missed considerations while building:
- AIO's were extremely loud (our master bedroom is located behind the inverter wall), so I had to modify the fan control of all 18 fans in all 6 AIO's to enable a temperature controlled fan speed. Because they heat up quickly under charging conditions, I had to implement an active equipment cooling on top of this to make them really quiet. To achieve this, I've installed a 9,000 BTU ducted mini split which cooling power is controlled via smart home rules, depending on the AIO temperatures. Now they are usually around 50-52°C, even under high load (charging and inverting).
- I've implemented an emergency shutdown circuit (I wanted to have that to be able to sleep with a better feeling) which shutdown the system in case of smoke detection or too high AIO temperatures or too high battery temperatures or camera detects fire or manually remote if I want. In case of an emergency is detected, the PV modules are shutdown via TIGO module level PVRSS, the batteries are disconnected from the AIO's via 600A relays, the AC-in's are disconnected from the grid via contactor if connected (usually the are always disconnected anyway). Because these three different types of disconnect's are NO (normally open) operated, I've needed to build a blackstart UPS to initially startup the system.
I am totally amazed and very pleased that my LED pulsing/flickering problems are completely gone - without doing anything! While in building phase, I've noticed the LED pulsing problem a couple of times and I thought many hours about how to solve it. I have no idea why this problem completely disappeared, independent if solar production or not, clouds or not, battery charging or discharging, high or low load,...
I'll update this thread from time to time with new pictures, findings, data, issues, etc.