We live in South Australia ... on grid ... but want to put in an off-grid system ... retaining the grid for backup and for battery charging when necessary.
I've collected 12.6Kw of used panels (6Kw of 250 watt panels and 6.6Kw of 275 watt).
I've organised a 14Kw LF inverter and am chasing up a large 48V traction or forklift battery.
What I'd like some help with is in deciding where to locate all the ancillary equipment ... and what extra bits I need to plan locations for.
The diagram shows the property layout, orientation and some dimensions.
There's not much doubt that the panels would be best on the north facing roof of the shed, which fortunately has zero shading due to a large empty paddock alongside.
My main question is around the best location for charge controllers, inverter and battery etc.
There are several options for where they could go but I'm leaning towards inside the shed and below the panels ... position 1.
There is an adjoining shed (large farm style shed) with open front that would be 'safer' perhaps ... but with the extra distance from the panels would add considerably to cable expenses and voltage drop. Especially as we'll have lots of strings of just 3 or 4 panels.
The last option would be to locate them at the opposite corner of that 2nd shed where the meter box is ... but thats another 20 metres or so ... and while it'd save on AC cabling, the DC cabling would be a major issue.
I plan to employ a solar tech to do the installation but I really want to have worked out the best locations for everything in advance ... rather than potentially getting talked into changing things and regretting it later.
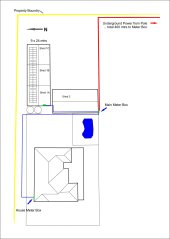

I've collected 12.6Kw of used panels (6Kw of 250 watt panels and 6.6Kw of 275 watt).
I've organised a 14Kw LF inverter and am chasing up a large 48V traction or forklift battery.
What I'd like some help with is in deciding where to locate all the ancillary equipment ... and what extra bits I need to plan locations for.
The diagram shows the property layout, orientation and some dimensions.
There's not much doubt that the panels would be best on the north facing roof of the shed, which fortunately has zero shading due to a large empty paddock alongside.
My main question is around the best location for charge controllers, inverter and battery etc.
There are several options for where they could go but I'm leaning towards inside the shed and below the panels ... position 1.
There is an adjoining shed (large farm style shed) with open front that would be 'safer' perhaps ... but with the extra distance from the panels would add considerably to cable expenses and voltage drop. Especially as we'll have lots of strings of just 3 or 4 panels.
The last option would be to locate them at the opposite corner of that 2nd shed where the meter box is ... but thats another 20 metres or so ... and while it'd save on AC cabling, the DC cabling would be a major issue.
I plan to employ a solar tech to do the installation but I really want to have worked out the best locations for everything in advance ... rather than potentially getting talked into changing things and regretting it later.
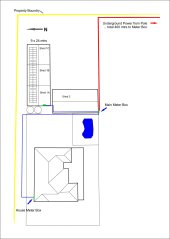
