Hi,
So i have just completed my first DIY build of two EEL 48V (16s) cases and are using them in parallel with my Victron Quattros (VenusGX).
But when i enable the NEEY (4A Active) balancer the Seplos BMS goes bananas and reports completly wrong voltages per cell.
I have disabled balancing in the BMS.
I have also verified the true/correct voltage on the cells with my multimeter (Fluke 179), and that is the same as the NEEY is showing.

Is this normal or has anyone else experienced the same issue?
Kind Regards
MrSwede
So i have just completed my first DIY build of two EEL 48V (16s) cases and are using them in parallel with my Victron Quattros (VenusGX).
But when i enable the NEEY (4A Active) balancer the Seplos BMS goes bananas and reports completly wrong voltages per cell.
I have disabled balancing in the BMS.
I have also verified the true/correct voltage on the cells with my multimeter (Fluke 179), and that is the same as the NEEY is showing.
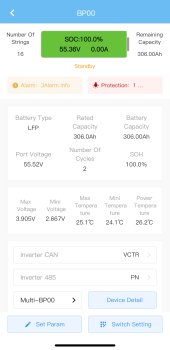


Is this normal or has anyone else experienced the same issue?
Kind Regards
MrSwede