JeepHammer
Solar Wizard
- Joined
- Nov 15, 2019
- Messages
- 1,149
Dielectric grease is non conductive and if used properly and in the appropriate circumstances okay as long as it does not form an insulating layer between & amongst the conductors and the connection. ~ When a manufacturer provides a wire terminal connection on a device it is unwise to take it upon ourselves to modify and exceed the gauge, therefore, potential amperage of the connector as built.
You are certainly free to do what you think is right.
There are places I won't use grease, it's simply not needed,
Other places it not appropriate.
Consumer 'Battery Cable' is thicker stands (opposed to something like welding cable) and I find the strands mash the grease out at contact points, but stays between strands where moisture can enter/corrode.
In most cases,
Manufacturers don't apply things like Never-Seize, Thread Locker, Oxidation Guard, Dielectric Grease simply because it costs time & money.
Anyone that's ever had to work on an old vehicle or equipment is most certainly aware of rusted/corroded in bolts, corroded out electrical connectors, twisted off fasteners, etc...
For instance, I won't put a steel bolt in aluminum without either thread locker (seals out moisture as well as keeping the bolt in) or Never-Seize to keep that bolt from galvanic corrosion lock into the aluminum.
I've got 3 aluminum engine timing covers with water pump bolts twisted off in them right now in the shop, the flowing coolant increases the galvanic issues and bolts ALWAYS corrode solidly into these timing/pump covers.
While it's a steady income stream for me, it takes very particular tools to repair those covers, which are for 'Vintage' engines not made since 1990.
Any & every outdoor electrical connection I do gets protected.
Aluminum cables get Oxi-Guard when they clamp in lugs,
Copper wires get tinned, Oxi-Guard, or Dielectric grease.
I learned this the hard way, since humidity, fog, rain gets everywhere no matter what, and DC electrical connections don't handle it well, much worse than AC wiring.
It's like the guff I take about lead/acid battery connections, solid, plated connector, heavy crimp (mechanical connection), silver bearing electrical solder, then glue filled heat shrink tubing...
Then seal up between battery post & case with the spray on goop, make connection, and spray everything to seal it up.
While other people schedule regular replacement ends, I clean mine every year or two, seal them back up and some have been around for 15 years (or more).
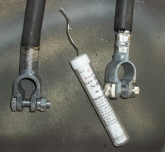
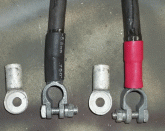
THIS is what happens when just moisture/water gets into a terminal/cable bundle...
And this should explain WHY I learned to seal everything up against DC & moisture.
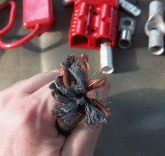